In the realm of military and defense equipment testing, as well as in industries with high standards for product reliability, the need for comprehensive and accurate environmental and mechanical stress testing is non-negotiable. The customized climatic chamber combined with a vibration shaker test device, which meets MIL STD-202g Method 201A requirements, emerges as a crucial solution for ensuring the performance and durability of various components and systems.
This advanced testing apparatus is designed to subject test samples to a combination of temperature, humidity, and vibration stresses in accordance with the stringent guidelines of MIL STD-202g Method 201A. It serves military contractors, aerospace manufacturers, and other industries where products must endure extreme and diverse environmental conditions. The primary objective is to evaluate how well the samples can withstand the simultaneous or sequential application of climatic and mechanical forces, thereby identifying potential weaknesses, optimizing designs, and ensuring compliance with military and industry standards.
- Robust and Insulated Chamber Construction
- Precision Temperature and Humidity Control System
-
- Powerful Vibration Shaker
- Synchronized Control and Data Acquisition
- Compliance with MIL STD-202g Method 201A
- The equipment is specifically calibrated and programmed to perform tests in strict accordance with MIL STD-202g Method 201A. It can replicate the specific temperature and humidity cycling, vibration profiles, and test durations specified in the standard. This ensures that the test results are valid and comparable, allowing manufacturers to make informed decisions about product design, material selection, and quality control. The chamber also provides a means for documenting compliance with the standard, which is essential for product acceptance in military and defense applications.
Shaker Specifications
Rated Sine/ Random/ Shock Force | 1,100 kgf/1,100 kgf/2.200 kgf | Armature Mass | 11kg |
Frequency Range | 5-3.000 Hz | Inserts Size (Standard) | M8 |
Max./Continuous Displacement p-p | 51 mm/ 51 mm | Load Attachment Points (Standard) | 17 |
Max. Velocity | 2.0 m/s | Natural Frequency-Thrust Axis | <3Hz |
Max.Sine/ Random Acceleration | 100/60g | Mac Vertical Load Support | 300 kg |
Armature Diameter | 235 mm | Stray field @ 152 mm above table | ≤1mT (10 gauss) |
Fundamental Resonance frequency | 2,500 Hz (nom.) ± 5% | Dimension LxWxH | 940 mmx715 mmx780 mm |
Allowable Armature Overturning Moment | 300 Nm | Weight (Uncrated) | 1.000 kg |
PA10K Power Amplifier Specifications | Blower Specifications |
Rated Output Capacity | 10kVA | Bl ewer Power | 4kW |
Signal to Noise Ratio | ≥65 dB | Air Flow | 0.38 m3/s |
Amplifier Efficiency | ≥90% | Air Pressure | 0 048kgf/cm2 |
System Protection | Multiple | Air Duct Diameter/ Length | 120/4000mm |
Dimension (Uncrated) LxWxH | 610mmx900mmx 1,550mm | Dimension (Uncrated) LxWxH | 610mmx750mmx 1,450mm |
Weight (Uncrated) | 400 kg | Weight (Uncrated) | 120Kg |
Chamber | Dimensions (mm) |
Capacity | 512L |
Inner Chamber Dimensions | 800×800×800mm (W width × D depth × H height mm) |
Temperature Range | -40℃~+150℃ |
Cooling Rate | +20℃~-40℃ Average throughout the range: 2℃/min |
Humidity Range | 20%RH~98%RH |
Overall Dimensions | 1200×2500×1500 (W width × D depth × H height mm) excluding lifting table dimensions |
Weight | 1500kg |
- Aerospace and Defense Electronics
- A leading defense electronics manufacturer used the system to test a new generation of communication equipment for military aircraft. The tests involved subjecting the equipment to extreme temperature and humidity conditions while simulating the vibrations experienced during flight. The results revealed a potential issue with the soldering joints of a circuit board, which could have led to a communication failure during a mission. By redesigning the circuit board and using more reliable soldering techniques, the manufacturer was able to enhance the reliability of the equipment and ensure its proper functioning in the harsh military aerospace environment.
- Military Vehicle Components
- A manufacturer of military vehicle parts tested the durability of their new engine mounts in the chamber. The mounts were subjected to a combination of high temperatures, humidity, and intense vibrations. The tests showed that the original design had a limited lifespan under these conditions. By modifying the material composition and the structural design of the mounts, the manufacturer was able to increase their durability and reduce the risk of engine misalignment and vibration transfer, improving the overall performance and reliability of the military vehicle.
- Weaponry and Ordnance
- A military ordnance manufacturer tested the performance of a new type of firearm under various environmental and mechanical stress conditions. The firearm was exposed to rapid temperature changes, high humidity, and vibrations similar to those encountered in combat situations. The tests identified a problem with the firearm's firing mechanism, which was affected by moisture and vibration. By making design improvements and using more corrosion-resistant materials, the manufacturer was able to enhance the firearm's reliability and accuracy, ensuring its effectiveness in the field.
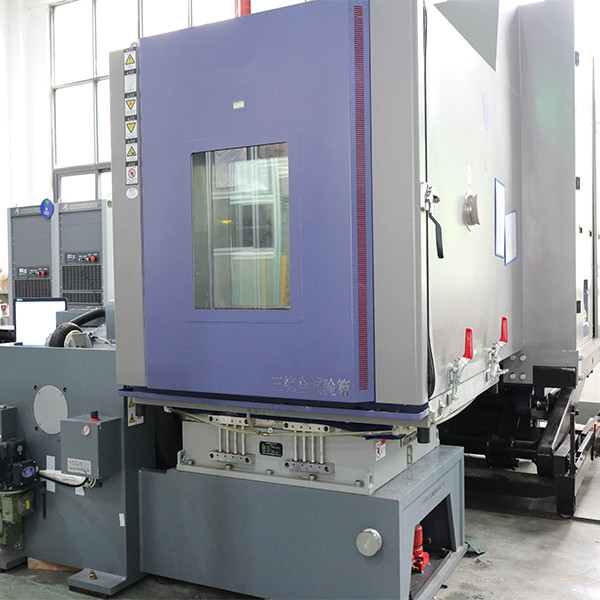
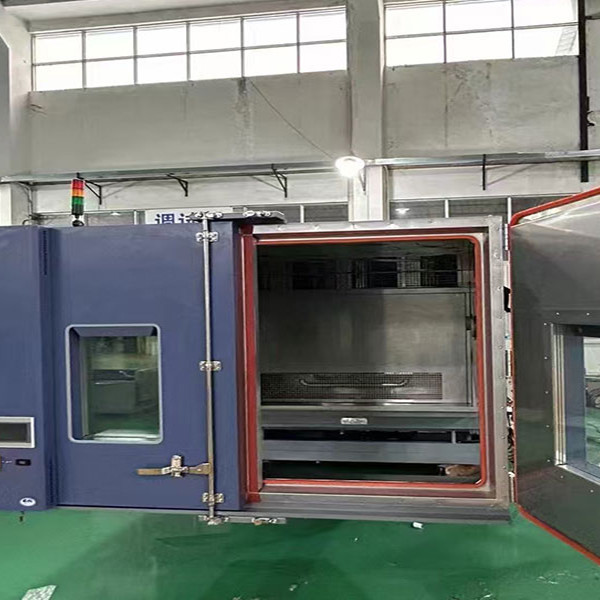
The customized climatic chamber combined with a vibration shaker test device that meets MIL STD-202g Method 201A requirements is an essential asset for any organization involved in military and defense equipment testing, product development, quality control, and research. If you are looking to enhance your testing capabilities, ensure compliance with military standards, or drive innovation in military product design, this is the ideal solution. Contact us today to learn more and get a customized quotation. Let us help you unlock the full potential of your military testing and research efforts.